Explore the ultimate 2025 guide to metal roofing. Learn about cost, types, installation, pros and cons, and how to choose the best roof for your home.
Table of Contents
Introduction
Today we’ll look at how metal roofing is no longer just an option in the U.S.—it’s quickly becoming the most trusted roofing solution. The total roofing market size reached around $23.35 billion last year and is expected to grow at an annual growth rate of 6.6% over the coming decade.
Nearly 62% of roofing contractors expect metal roofing sales to increase in 2024, clearly reflecting changing homeowner preferences. The biggest reason for this is longevity, safety protection, and energy savings—what every homeowner wants today.
Who is this guide for?
- People looking for alternatives to asphalt shingles
- Homeowners upgrading an existing roof
- First-time metal roof installation
- Builders or architects looking for sustainable, energy-efficient solutions
In this guide, we’ll cover:
- What metal roofing is and its types
- Advantages and disadvantages
- Costs in 2025 – breakdown, installation costs
- Which metal to choose and why
- U.S.-specific tips, climate considerations, and resale value
2.H2 What Is Metal Roofing Really
Definition and Basic Understanding
Metal roofing is a roofing system that uses sheets of metal—such as galvanized steel, aluminum, copper, and zinc—in the form of panels or shingles and is applied to the roof with secure fastening methods. This system can withstand extreme weather, fire, and UV rays, with a lifespan of approximately 40–70 years, which is much longer than typical asphalt shingles.
Residential vs. Commercial Uses
Residential: Homes typically use standing seam, metal shingles, or stone‑coated panels for aesthetics. These are primarily utilized on sloped roofs and enhance the visual attractiveness.
Commercial: Commercial buildings use plain sheet panels and exposed-fastener systems on flat or low-slope roofs. Their strength, low maintenance, and HVAC/solar compatibility make them popular.
Basic Metal Types
- Steel – Available in Galvanized or Galvalume form, strong and rust-resistant.
- Aluminum – It is lightweight, resistant to corrosion, and ideal for coastal settings.
- Copper – premium look, natural patina, and 70–100+ year durability.
- Zinc – self-healing with a natural coat and more eco-friendly but expensive and less available.
Each of these metals has its own pros—like rust resistance, longevity, and aesthetics—and some cons—like cost, dents, availability—depending on your roofing needs, location, and budget.
H2 Types of Metal Roofing Materials With Pros Cons and Price
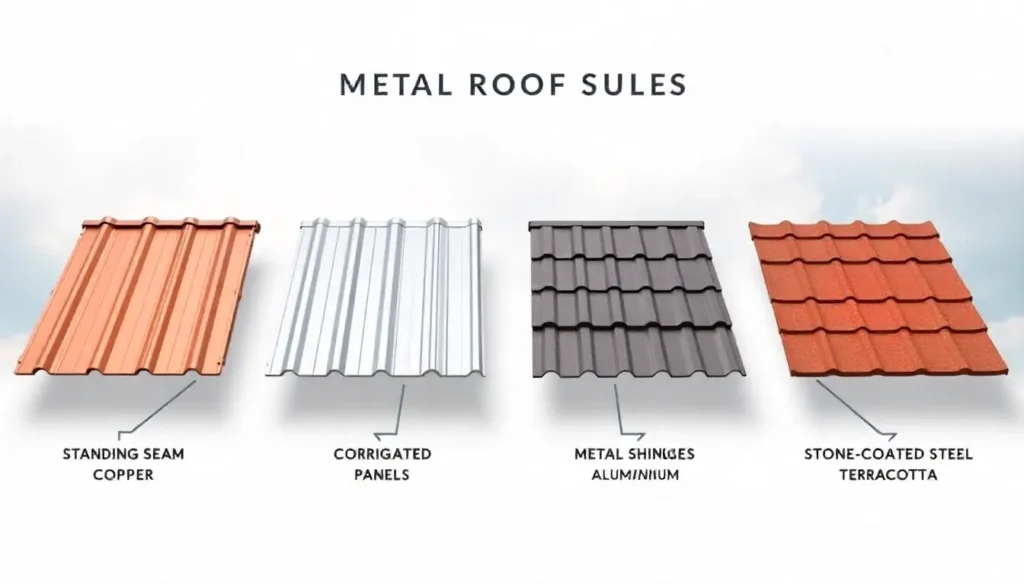
Now let’s see how many types of materials are used for roofing. Generally, the decision of which metal roofing material to choose depends on your need, area, budget and design preferences. Here is a comparative analysis of the top 6 materials:
Galvanized / Galvalume Steel
Pros : Most economical; zinc-aluminum coating protects against rust and corrosion
Good performance in heavy weather, high availability
Designed to last 40–60 years
Cons : May corrodes more accidentally in coastal areas
Cost may increase slightly if high-end coatings are used
Cost : Material: $4–$10/sq-ft
Installed: $8–$16/sq-ft generally; overall $5–$13/sq-ft for corrugated steel, $8–$20/sq-ft for standing seam steel
Best Use: Budget-friendly residential & storm-prone regions
Aluminum
Pros:
Lightweight, 100% recyclable, coastal corrosion-resistant
Lifespan 50+ years, reflectivity helps in energy efficiency
Cons:
Dents can easily form; UV can cause fading
Cost:
Material: $6–$12/sq-ft; Installation: $10–$17/sq-ft total
Averages ~$7–$17 installed
Best Use: Coastal homes, moderate-weather regions
Corrugated Metal (Steel/Aluminum)
Pros:
Most economical option, strong ripple design, rustic appeal
Energy-efficient and recyclable
Cons:
Increases leak risk as fasteners are visible
Generally low aesthetic appeal
Cost:
Material $4–$10/sq-ft; Installed $5–$12/sq-ft
A $1,000sq-ft roof costs ~$4K–$14K
Best Use: Barns, sheds, DIY projects, rustic homes
Copper
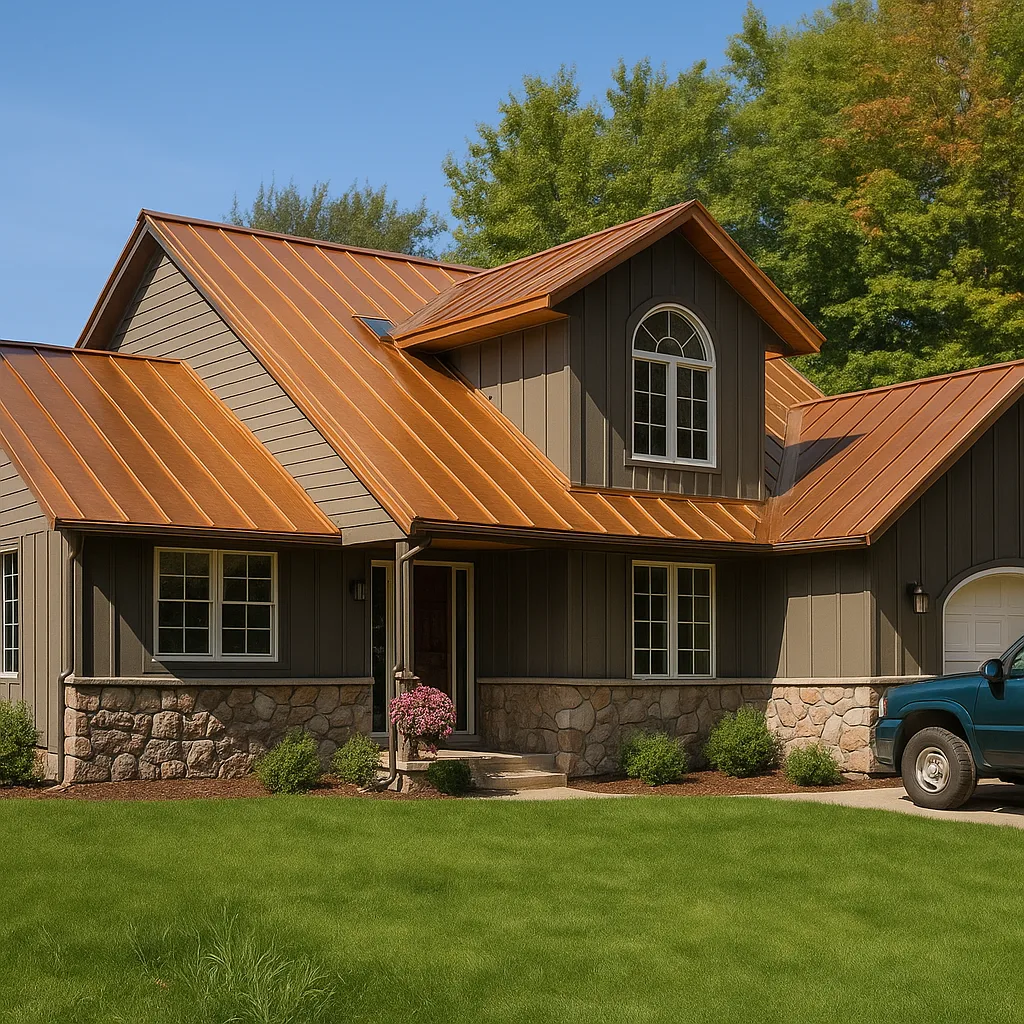
Pros:
Premium look, develops natural patina, low maintenance, 70–100+ year lifespan
Corrosion-resistant and recyclable; a favorite in historic homes
Cons:
Most expensive option, installation also expensive and requires skilled installers
Cost:
Material: $15–$25/sq-ft; Installed: $20–$35/sq-ft
The total cost of a 2,500sq-ft roof ranges from $50K–$100K
Best Use: High-end homes, architecturally significant projects
Zinc
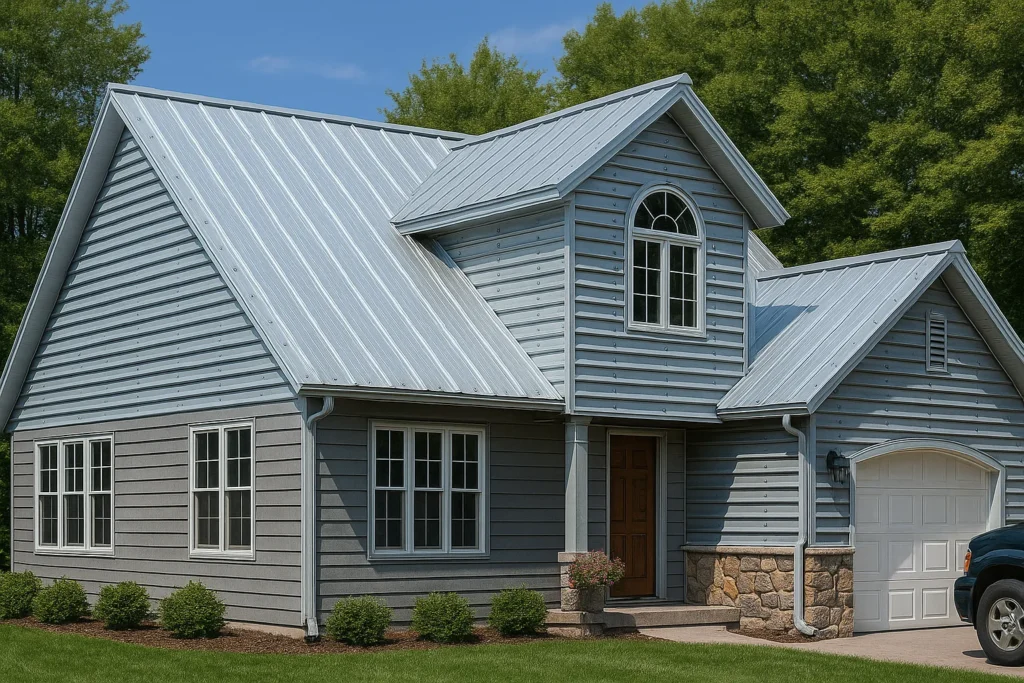
Pros:
Self-healing surface, patina formation, non-corrosive, very environmentally friendly, typical lifespan 80–100 years
Cons:
Expensive, limited US availability, installation expertise required
Cost:
Material: $12–$20/sq-ft; Installed: $14–$25/sq-ft (Standing Seam), $5–$7/material installed corrugated)
A small roof can also cost $19–$35/sq-ft.
Best Use: Sustainable buildings, eco-focused architectural designs
Standing Seam Metal (Steel, Aluminium, Zinc, Copper)
Pros: Reduced risk of leakage thanks to hidden fasteners, featuring a stylish modern look Solar compatible; premium look longevity
Cons: The most expensive installing system; requires professional installers
Cost: Steel: $8–$16 installed; Aluminum: $10–$17; Zinc: $14–$25; Copper: $20–$35
Best Use: Contemporary homes, high ROI
projects, solar-ready roofs
Materials | Lifespan ( years) | Installation cost/ sqft | Ideal use |
Steel | 40-60 | $8-$16 | Budget homes, Harsh climate |
Aluminum | 50+ | $10-$17 | Coastal, light weight needs |
Corrugated | 30-50 | $5-$12 | Rustic, utilitarian structures |
Copper | 70-100 | $20-$35 | Primium, architectural statements |
Zinc | 80-100 | $14-$25 | Sustainable, long-term projects |
Standing seam | 40-70+ | $8-$35 ( varies by metal ) | Mordan and energy-efficient design |
The choice of metal roofing depends on your preferences and budget:
Steel or corrugated are best for budget + storm resistance.
Aluminum is best for coastal properties.
Copper or Zinc are best if you want luxury and longevity.
Standing Seam is on top for modern curb appeal and solar compatibility.
After knowing the reality and estimated cost of all these materials, you can choose the best option as per your need and style.
4.H2 Key Benefits of Metal Roofing
Longevity & Durability
Metal roofing systems are recognized for their durability.
A properly installed and maintained metal roof can last anywhere from 40 to 70 years — and in certain instances, even up to 100 years.
It is able to withstand harsh weather conditions such as high winds, heavy rain, hail, and snowfall, making it very useful in areas where the weather is often challenging.
Energy Efficiency
Thanks to reflective coatings and cool-metal technology, these roofs reflect a lot of the heat back into the air. This can reduce summer AC bills by 10–40%. Studies by DOE’s Oak Ridge National Laboratory also found energy savings of up to 40% on average.
Low Maintenance & Safety
Metal roofs resist mildew, rot, and insect-damage thanks to a rust-resistant coating, which reduces long-term repair costs. Plus, they are ClassA fire-resistant and safe to use with lightning.
Eco-friendliness & Recyclability
These roofs are constructed using recycled materials, and once they reach the end of their lifespan, they can be fully recycled. This reduces landfill waste and lowers the environmental footprint.
Resale Value & ROI
Reports like Remodeling Magazine found that metal roofing has a national average ROI of 48%; as high as 60–85% in some areas. According to Angi, a new roof can increase a home’s resale value by $7,000–$8,100. Apart from this, the curb appeal and buyer interest of the properties also increases.
Insurance Benefits & Long-Term Savings
Metal roofs that are rated for weather and fire typically lead to lower insurance premiums because they present a decreased risk. Plus, the long-term cost savings due to energy savings and durability often justify the initial investment.
Bottom line
In 2025, a metal roof is an economically and environmentally sensible choice—because it offers longevity, energy savings, low maintenance, environmental sustainability, and high ROI. For homeowners who want durability, aesthetic, and financial value, this roofing solution is the most promising option.
5.H2 Major Disadvantages You Should Know
High Initial Cost
Metal roofs have an initial cost 2–3 times higher than asphalt shingles, especially if you choose premium metals. For example, the installed cost of a standing-seam steel roof can be as high as $15 per sqft while shingles are available for around $5/sqft. While this expense may be balanced out by energy savings and replacement costs in the long run, the upfront investment may be challenging for some homeowners.
Noise During Rain/Hail
Ferrous metal roofs can produce exceptionally loud noises during rain and hailstones. Some people consider it calming, while others perceive it as disturbing. Although this can be largely minimized with acoustic underlayment and attic insulation, some noise may still escape.
Dent and physical damage (Dent Susceptibility)
Soft metals, such as aluminum and copper, can be easily dented by hailstorms or fallen tree branches. This affects the aesthetics of the roof and even minor dents can be noticeable. Some warranties do not cover cosmetic damage, and repairs can cost hours and money.
Expansion & Contraction
Metal parts expand and contract with ground temperature, which can loosen fasteners and cause leaks in seams. Installation reliability can be low if proper technique and high-quality fasteners are not used.
Complex Installation
Installing metal roofs is specialized work. Incorrect fitting or non-standard underlayment can cause leaks, ventilation issues and premature roof failure. Many HOAs also don’t allow it due to outdated aesthetics, which can add time to approvals and installation.
Other Issues
Corrosion: Salt-laden air in coastal areas can corrode metal, especially if there’s no protective coating underneath.
Slippery surface: The roof can be slippery when it rains or snows, making maintenance risky.
Color fading and chalking: Coatings can fade or chalk over time, reducing cosmetic appeal.
Bottom line
Metal roofs, while professional and sturdy, can have downsides up front, such as being expensive, noisy, prone to dents, or technical installation requirements. If you examine these aspects carefully and install them correctly, this investment can live up to your expectations in the long run.
6.H2 Cost of Metal Roofing in 2025 Full Breakdown
Average Cost by Material Type
Galvanized/Galvalume Steel: Installed cost $6.50–$13.50/sqft
Aluminum: $8–$16/sqft installed
Standing Seam (steel/alum/zinc/copper): $9–$16/sqft installed; premium metals may reach $20+/sqft
Copper: $15–$22/sqft installed
Zinc: $11–$17/sqft installed
Labor & Installation Charges
- Nationwide, labor accounts for ~$4–$8/sqft (i.e., 40–60% of total cost), with higher rates in urban or high-cost regions.
- Technical systems like standing seam require experienced crews, increasing labor cost further.
Cost by Roof Size & Pitch
- For a standard 1,700sqft home, total installed cost averages $10,940–$16,722 per This Old House data.
- Bigger roofs reduce per-foot cost; smaller/complex roofs or steep pitches add additional $1–$5/sqft for tear-off and safety gear.
- Roofing “square” (100sqft) concepts apply; steep or curved roof increases both labor and material wastage.
How to Save Money on Metal Roof Installation
- Off-season scheduling: Fall/winter bookings are often 5–15% cheaper
- Order in bulk: Sheet and accessory orders in volume attract supplier discounts
- Utilize the current roof deck: Avoid tear-off whenever feasible to save $1–$5 per square foot.
- Rebates & incentives: Federal/state energy credits can reduce costs by $200–$1,500
- Get multiple quotes: Compare at least three licensed contractors to ensure you’re paying market rates
Bottom line
The installed cost of Meta roofs ranges from $6–$16/sqft ($20+ on premium types). Roofing material, labor, roof size, pitch, and premium finishes are determinants. While the initial expense may be greater, the durability, energy efficiency, and potential resale value render it a wise investment for the long term.
7.H2 Metal Roofing and the Environment
Recyclability of Roofing Materials
Metal roofs are made up of a minimum of 25% recycled materials and can be fully recycled at the end of their lifespan. When these roofs reach the end of their lifespan, or if a replacement is required, the old material can be sent to recycling plants rather than to a landfill.This significantly lowers the extraction of resources and the energy consumption linked to it.
Rainwater Harvesting Compatibility
The smooth, non-porous surface of metal roofs is ideal for rainwater harvesting. Rainwater drains easily into a collector system without contaminants, allowing water to be collected for irrigation, landscaping or non-potable uses.
Sustainable Manufacturing Practices
Today’s eco-conscious manufacturers use recycled metals (25–90%), and ash-saving coatings (low VOC) are used. Moreover, metal roofs are lightweight—approximately 50% the weight of asphalt—resulting in energy savings during both manufacturing and transportation.
Contribution to Net‑Zero Energy Homes
Cool roof coatings cause metal roofs to reflect extreme heat, reducing cooling loads. An Oak Ridge Labs study found indoor energy savings of approximately 40%. When combined with the insulation, solar systems, and energy efficiency needed for Net‑Zero or Passive homes, metal roofs are especially impressive.
Bottom line
Amid growing environmental challenges, metal roofing proves to be a sustainable choice—it’s recyclable, rainwater-compatible, low-carbon manufacturing, and energy-efficient. This is a roofing solution that contributes towards a better environment not only now, but also for future generations.
8.H2 Metal Roofing and Climate Considerations
Suitability in Hot Climates & Reflectivity
High-reflectivity coatings (cool-metal finishes like Kynar 500) trap heat like fabric, reducing surface temperatures up to 50°F (28°C).
A DOE study indicates that reflective metal roofs can lower energy expenses by 10–40%, offering considerable savings on cooling costs.
Suitability in Cold Climates & Snow Shedding
Snow and ice slide off smooth metal surfaces, reducing the risk of heavy snow accumulation.
Properly designed floating clip systems and steep pitches prevent ice dams, while gained heat is channeled away from the rooftop without damaging the structure.
Salt Resistance in Coastal Areas
Galvalume and aluminum coatings cope better with coastal salt exposure—Galvalume has exceptional corrosion resistance, while galvanized steel shows deterioration earlier.
Aluminum roofs are lightweight and rust-proof, providing cross-season durability in increased coastal humidity.
Fire Safety in Wildfire Zones
Metal roofs are non-combustible and have a Class A fire safety rating, making them ideal in wildfire-prone regions.
Metal roofs are lightweight, allowing firefighters to contain the structure from within, improving fire control.
Bottom line
Hot/urban zones: Cool coatings + reflective pigments save on cooling bills.
Cold/snowy areas: Smooth surfaces and correct roof pitch prevent ice dams.
Coastal homes: Better salt resistance from Galvalume or aluminum.
Wildfire zones: Class A fire safety and enhanced protection from non-combustible materials.
Metal roofs offer durability and performance in all climates—it just takes the right material, finish, and installation.
9.H2 Metal Roof vs Asphalt Shingles What to Choose
Aspect | Metal roofing | Asphalt shingles |
Initial cost | Higher ($6-$16 per sqft) | Lower ($4-$9 per sqft) |
Lifespan | 40-70 + years | 15-30 years |
Energy efficiency | Up to 20-40% saving with cool coatings | Basic level,hit absorbing |
Durability | Withstends 140+ mph wind, class A fire rated | Moderate resistance to wind/fire |
Maintenance | Low maintenance, minimal repairs | Requires periodic replacement & upkeep |
Environmental impact | 100% recyclable, low waste | Petroleum – based ends up in |
Which is better?
If you want a long-term, low-maintenance, energy-efficient and high-ROI roofing, a metal roof is the better choice.
For homeowners with budget constraints or short-term housing plans, asphalt shingles are a practical option, but they can cost more than metal roofs due to their faster lifespan.
10.H2 Installation Process Explained
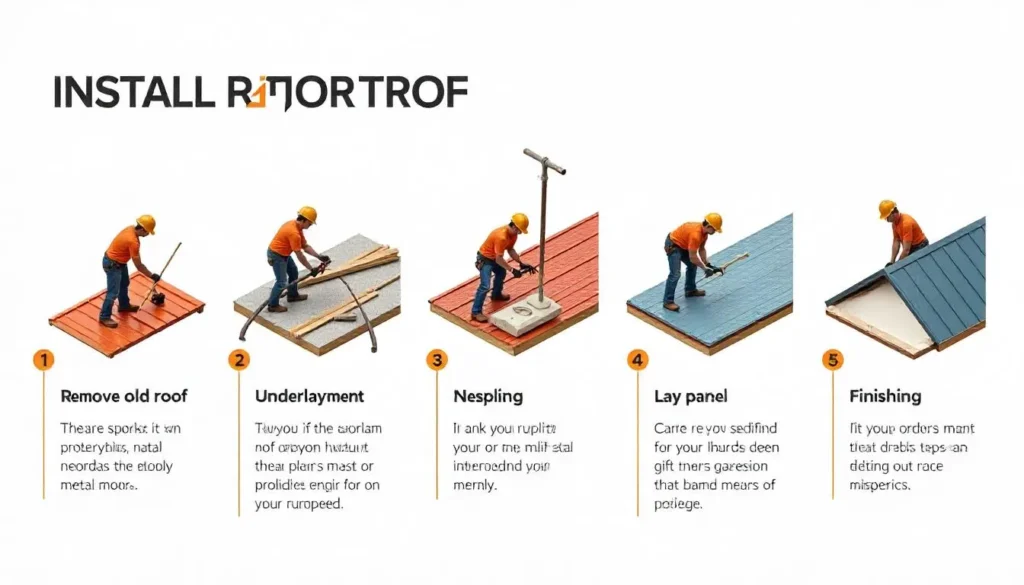
Step-by-Step Installation Timeline
- Inspection & Prep (1‑2 days): Entire roof is inspected, deck condition, ventilation and underlayment are assessed.
- Tear‑Off or Overlay (1 day): Old shingles are removed or in approved cases new metal can be applied directly over old shingles (turn0search0, turn0search4).
- Underlayment + Flashing (1 day): Synthetic underlayment or ice-and-water barriers are applied to prevent moisture and thermal movement.”
- Panel Installation (1–2 days): Metal panels are precisely installed with fasteners or concealed-seam clips.
- Final Inspection & Cleanup (1 day): All clips, nuts secured, flashing sealed and attic checked.
Tools and Techniques
Tools: Metal shears, torque screwdrivers, angle grinders, seamers for standing‑seam
Techniques: Floating clip systems to accommodate expansion, concealed fasteners to prevent leaks
Safety gear: Fall arrest anchors and protective footwear on slippery surfaces (turn0news12, turn0search11).
Install Over Existing Roof?
Yes, if old shingles are in 1 layer and decking is solid, this method saves $1–$2/sq ft (turn0search4).
But moisture trapping, warranty voiding and ventilation issues must be avoided (turn0search2, turn0search7).
How to Find a Certified Contractor Select
- Experience: 5+ years of experience in metal roofs and neighborhood references
- Licensing & Insurance: Workers compensation and liability insurance mandatory
- Manufacturer certification: Certified training from brands like Fabral, Drexel, Englert
- Warranties: Protection for materials, workmanship, and conditions of “no tear-off”
Bottom line
Metal roof installation is very structured—starting with inspection and prep, to panel fastening, flashing, guided safety practices, and certified installer. And if you can salvage old asphalt shingles, it’s possible to save $1–$2/sq ft on installation cost in an approved scenario.
11.H2 Maintenance Tips to Extend Metal Roof Life
Yearly Inspections and What to Check
Examine the roof a minimum of twice annually (in spring and fall). Check for: loose or missing fasteners, sealant cracks, damaged flashing, and rust spots. Also check for water stains, mold or leak evidence from the attic.
Cleaning Tips and Safe Products
Remove leaves, algae or debris with a soft brush or low‑pressure water spray. Use a mild detergent or approved cleaner. High-pressure washing or bleach may damage coatings.
When and How to Repaint or Recoat
Clean rust spots with a wire brush, then apply a rust‑inhibiting primer and recoat with matching metal paint.
Paint fading or chalking—apply manufacturer-approved roof paint, recoat every 10–15 years.
Fixing Minor Leaks and Dents at Home
Minor leaks: Insert rubber-gasketed screws into screw holes, apply silicone sealant on both sides—Reddit recommends “replace screw with rubber washer + sealant.”
Dents (hail or branch-induced): FAQ says “Dry ice dent removal” or gently press out is possible. Minor cosmetic dents are usually safe.
Bottom line
These four steps—twice-daily inspection, safe cleaning methods, timely repainting, and DIY fixes for minor leaks and dents—will keep your metal roof in good condition and long life for decades.
12.H2 Common Myths About Metal Roofing Busted
Myth 1: Metal roofs attract lightning
Reality: This claim is false. Research shows that lightning is affected by height and surrounding buildings, not roofing material. Because metal is non-combustible, lightning safely dissipates to the ground when struck, reducing fire hazards.
Myth 2: They rust easily
Reality: Modern metal roofs such as Galvalume, aluminum, or Kynar-coated steel have zinc-aluminum layering and protective coatings. These coatings prevent rust and typically protect the roof for 40–70 years.
Myth 3: They look too industrial or outdated
Reality: Today’s metal roofs, especially in residential designs, come in wood-look, matte finishes, and tile-style shingles. They fit well with many architectural styles—traditional, modern, farmhouse—and also increase curb appeal.
Myth 4: You can’t walk on them safely
Reality: Properly installed standing-seam roofs are safe to walk on. It’s important to wear soft-soled shoes and walk on seams or reinforced sections. Most metal panels are dent-resistant, and manufacturers often provide clear directions for walking.
Bottom Line:
These myths are simply misconceptions. With the latest technology and proper installation, metal roofs are a safe, durable, stylish, and peaceful option.
13.H2 Faq
Lifespan: How long does a metal roof last compared to shingles?
Metal roofs generally have a lifespan of 40 to 70 years, whereas asphalt shingles last between 15 and 30 years. This becomes a long-term investment.
Cost vs Value: is metal roofing more expensive upfront?
Yes, metal roofs have a higher upfront cost, but low maintenance, energy savings, and long life make it cost-effective in the long run.
Noise: Are metal roofs noisy in rain or hail?
With proper insulation, metal roofs can be equal to or less noisy than shingles.
Over-shingle installation: can I install metal over existing asphalt shingles?
Yes, if local building codes and roof structure allow, a metal roof overlay over existing shingles is possible—this saves tear-off costs.
Weather resistance: How do metal roofs perform in extreme conditions?
Metal roofs show excellent resistance to wind, fire, hail, rot, and insects.
Eco-friendliness: Are metal roofs environmentally responsible?
Metal roofs contain recycled content and are 100% recyclable. Plus, they are energy-efficient.
14.H2 Final Thoughts Is a Metal Roof the Right Choice for You
If you plan to live in the same home for a long time, metal roofing is an excellent investment. Its longevity (40–70 years), energy savings, and low maintenance make it superior to asphalt shingles. Yes, it costs more up front, but the resale value and insurance savings more than make up for it.
Metal roofs also provide extra safety and durability in extreme climates (such as hail, wildfire, coastal zones).